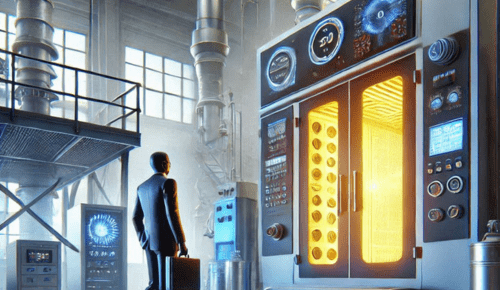
Powder coating is a meticulous process, and every stage counts. But cooling lag? That’s the silent disruptor no one talks about until it’s too late. When high-temperature powder coating ovens can’t cool down efficiently, the delay ripples through production, compromises coating quality, and even risks damaging parts. Tackling cooling lag requires a smart approach, and it’s not just about throwing in more fans. Here’s how to make your powder coating oven work smarter, not harder.
Optimizing Cooling Zones for Faster Temperature Transitions
Cooling zones in powder coating ovens are like pit stops in a race. They need to function efficiently to transition the parts from scorching heat to manageable temperatures without wasting time or energy. One common mistake is setting up these zones without considering how airflow and thermal gradients behave inside the oven.
By configuring zones strategically, you can create a smooth temperature drop without shocking the material or coating. A well-optimized cooling zone focuses on maintaining an even airflow across all parts, ensuring consistent cooling. Reliable powder coating ovens are designed to allow for modular adjustments in cooling zones, helping you tailor the process to your specific needs.
Careful attention to this step not only shortens overall cooling time but also reduces the risk of uneven cooling, which can lead to coating defects or warping. Investing in a quality powder coating oven with customizable cooling zones pays off in efficiency and results.
Incorporating High-capacity Ventilation Systems to Enhance Airflow
When it comes to cooling, ventilation systems are the unsung heroes. Without proper airflow, heat gets trapped, and cooling slows to a crawl. High-capacity ventilation systems can transform how a powder coating oven handles cooling, improving circulation and speeding up the process.
It’s not just about the size of the fans; the placement and direction of airflow matter even more. Compact powder coating ovens often require clever ventilation solutions to maximize airflow in tight spaces. With a high-capacity system, the heat dissipates faster, ensuring a uniform temperature drop across all parts.
Enhancing airflow doesn’t just address cooling lag—it also improves overall energy efficiency. A reliable powder coating oven with an optimized ventilation system works smarter, reducing downtime and ensuring parts exit the oven ready for the next step.
Using Advanced Heat Exchangers to Expedite Heat Dissipation
Heat exchangers are the technological backbone of modern powder coating ovens. These devices take the intense heat from the oven and transfer it out efficiently, speeding up the cooling process. When cooling lags, it’s often a sign that the heat exchange system isn’t up to par.
Advanced heat exchangers can handle high temperatures without faltering, making them essential for ovens dealing with heavy-duty coating tasks. The key is to select a system that matches the workload of your oven. Reliable powder coating ovens integrate these systems seamlessly, ensuring optimal performance without extra maintenance headaches.
Heat exchangers not only save time but also prevent energy wastage, keeping the cooling process both effective and eco-friendly. Investing in advanced technology here ensures your cooling system keeps pace with production demands.
Monitoring Temperature Fluctuations with Precision Control Systems
You can’t fix what you can’t measure, and that’s where precision control systems come into play. These systems monitor temperature fluctuations in real time, providing actionable insights to tackle cooling lag in your powder coating oven.
Accurate sensors detect when and where heat is building up or dissipating unevenly. Armed with this data, operators can adjust cooling settings on the fly, ensuring a smooth transition from the baking phase to cooling. Reliable powder coating ovens equipped with precision controls make it easier to identify inefficiencies and address them immediately.
Precision monitoring also prevents overcooling, which can be just as damaging as lagging temperatures. Striking the right balance ensures the coating cures properly, maintaining both the appearance and durability of the finish.
Designing Exhaust Pathways to Eliminate Trapped Heat Efficiently
Even the best cooling systems can struggle if the oven’s exhaust pathways aren’t designed to handle heat buildup. Trapped heat is a major contributor to cooling lag, as it slows down the overall dissipation process.
Exhaust pathways need to be wide enough to handle the oven’s workload but also strategically positioned to draw out heat efficiently. Quality powder coating ovens are engineered with this in mind, using custom exhaust designs to keep air moving smoothly. This prevents bottlenecks in heat removal, ensuring a steady drop in temperature.
If your current system isn’t performing, revisiting the exhaust pathway design might be the game changer you need. An efficient exhaust system ensures that cooling starts immediately, minimizing lag and improving overall cycle times.
Balancing Cooling Rates to Protect Part Integrity and Coating Quality
Rapid cooling might sound ideal, but it’s not always the best approach. Cooling rates need to be carefully balanced to protect the integrity of both the parts and their coating. Going too fast risks thermal shock, while a lagging system compromises efficiency and quality.
Reliable powder coating ovens are built with balancing mechanisms that allow operators to fine-tune cooling rates. This ensures that parts are cooled uniformly, avoiding stress points that can lead to cracks, warping, or uneven finishes. Compact powder coating ovens, in particular, benefit from these adjustments, as they often handle smaller, more delicate parts.
Balancing rates isn’t just about avoiding damage—it’s also about achieving consistent results. A well-cooled part exits the oven ready for inspection, with no surprises waiting further down the production line.